21.03.2022
BHUJODI WEAVE – THE TURBAN WEAVERS OF BHUJODI
The Indian state of Gujrat has long been the entry point to the Indian sub-continent and a major trade and learning centre between the rest of the world and the country.
Kutchi extra weft – Bhujodi is one of the crafts that have endured the test of time. Originally called Bhujodi after the town where it was born, a Bhujodi is the creativity of the Vankar or weaver who has learned the craft from his ancestors. Unlike other weaving techniques, it is characterized by very explicit motifs that are woven and create bold textures on the background-plain fabric, making it appear as if it is embroidered. The warp on the pit looms of bhujodi is manually wound, meaning it does not unwind as the weaver rolls the woven fabric like on handlooms with warps wound on warp beams.
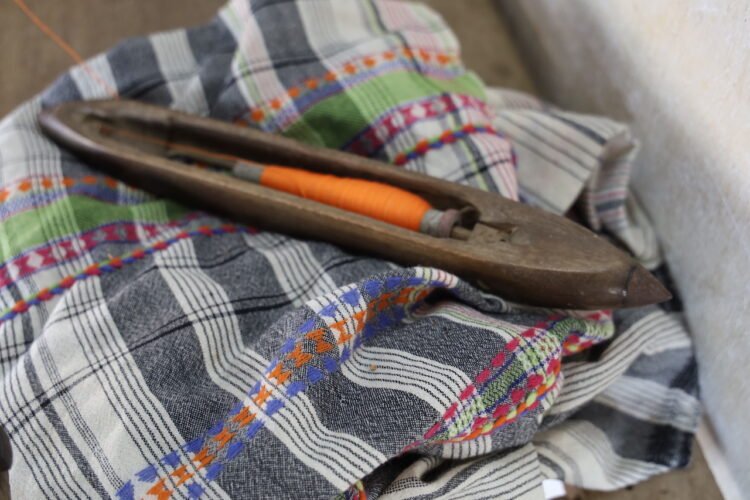
Details of Pachedi, extra weft technique used in Bhujudi weave
The Rabari community relies on the woollen veil cloths and heavy woollen blankets woven by descendants of Mughal migrants who migrated from Rajasthan 500 years ago. Hand-spun blankets were made by Bhujodi for the herdsmen to sheath and protect them in the open. These blankets were either draped over the shoulder or around the waist over Lungi and the horizontal linear weft motif details along the fabric in the lungi are known as pachedi and sometimes it was tied around the head like a turban.
The weaving process of the Bhujodi weave is followed by several intense processes. Weaving with the use of Varach or Patali is a tedious but very recognisable feature of the traditional Bhujodi weaving. While setting up the loom weaver would manually count the warp thread according to the standard patterns and put three to four flat wooden sticks behind the reed. These sticks lay flat while plain weaving and turned vertically to lift the warp for the extra weft ornamentation which runs selvedge to selvedge in a straight line. Lifting of these Patalis gives standard patterns such as Popati, Kanpopati, Hordi, Latha and many others. Weaving with the discontinuous extra weft is one of the very distinguishable features of the traditional bhujodi textile tradition.
Weaving in Bhujodi is done on the age-old pit looms with a very simple setup. Each wooden part of the loom is locally made by the carpenters for the Vankar community. The reed called Fani (फणी) is also handmade with bamboo sticks with gaping according to the thick or thinness of the yarn to be used. The four shafts (called Ranchh राच्छ) are hand made with nylon threads (substitute of cotton for long-lasting use) looped around sticks. The whole weaving process is a rhythmic movement of all these parts of the loom managed by the weaver. Both his legs manage four paddles for shedding while his arms are busy with the movement of the shuttle for the weft picks simultaneously. Almost every household in the Bhujodi village has a dedicated space for their looms. These spaces are mostly open and shaded small areas in a corner of the varanda with clean mud flooring. This setup gives us a fine example of a cottage industry in Indian villages, where these artisans work hard almost ten hours a day while staying in the comfort of their house and village.
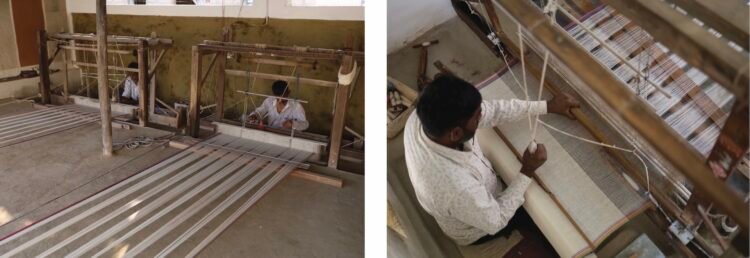
Pit loom used by the vankars of Bhujodi
Using a warped frame called Adano (अडाणो) is unique to the Kutch region. With the use of a long stick with a bobbin at one end for warp yarn to pass through, the weaver creates the length of the warp going from one wooden peg to another fitted on the frame. The distance between the two pegs gives a length of almost one and a half meters and accordingly required length is measured. The width of the fabric is measured by manually counting yarn ends. The crossing is also maintained while warping which later helps in drafting for the shedding of the warp yarns (up-down motion of the shafts, opening warp yarns for the weft to pass through). For setting up the loom, the new warp is joined on the remaining threads of the previous warp by twisting both ends using Wood ash for better grip. This process is locally called Sandhano (सान्धणो). After joining all the warp ends it is pulled through the head shafts and reed, It saves the time of new drafting and denting from the strat. Weaver deliberately leaves at least half a meter of warp yarn so that later it can be joined to the new warp of the same material that requires the same density of reed. The same twisting and joining process is done when a thread breaks while weaving. The twisting sometimes creates a little flote or a bump on the fabric surface which people might take as a defect but it is very commonly seen on handloom fabrics.
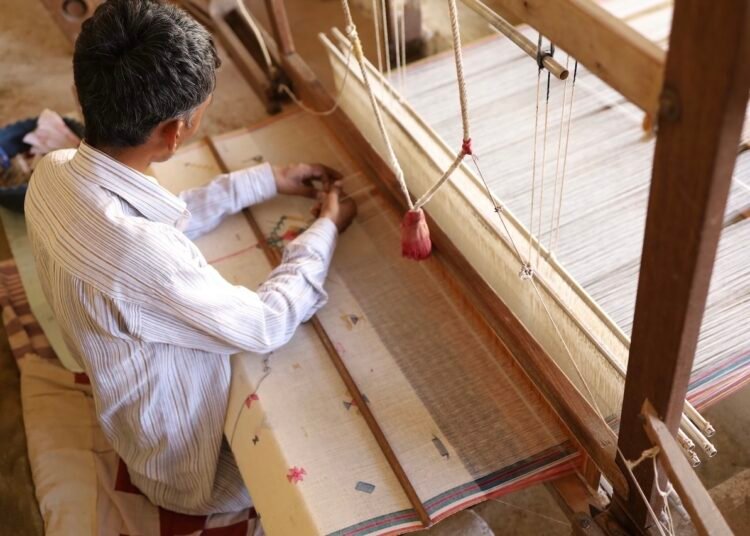
Vankar weaving motifs with extra weft technique
The entire process is like creating embroidery on the loom, which is a very time-consuming process and requires great skill and patience. Unlike the handlooms with warp winded on warp beams, where the warp unwinds as the weaver rolls the woven fabric, it is manually done on the pit looms of bhujodi. To roll the woven fabric the weaver loosens the rope tied to a pole next to him also called Ganesh (named after Lord Ganesha and worshipped as the main part of the loom). As soon as one length of the warp finishes the warp bundle is unwinded and tension is made even using the small wooden sticks and threads are untangled using Kulori, which is a brush made of tree roots found locally. This process is repeated over and over again until the warp finishes.
A closeup view of a motif created by the extra weft technique
The Selvedge of the fabric is also called Kor (कोर) locally. Other than the visual aesthetic Kor also has a technical purpose. It helps in achieving an even edge of the fabric. Usually, the fabric is woven with two yarn ends per dent but the Kor has just double, four yarn ends per dent which helps to hold the weft yarns and prevents loose edging. A very important part of the loom for weaving is Pandak (पड़क). It is two sticks tied together to adjust according to the width of the fabric and has two small nails on both ends which go in both selvedges. The purpose of this stick is to maintain the same width throughout the weaving process.
Typical to all handweaving traditions, a piece may take days to months, depending upon the intricacy and newness of the design. While weaving in kutch is mostly done by men, it is a collective effort of the whole family. A weaver simply cannot function on his own, without the support of the women in the family, who helps in making the bobbins from the yarn hanks or cones. They also help in making the warp.
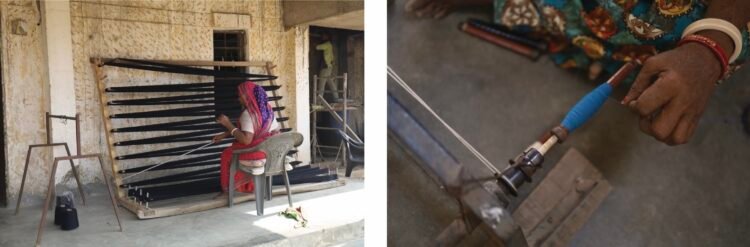
Women of the family involved in the weaving process of warping and winding bobbins from the yarn hanks
To survive, the Bhujodi craft has today changed drastically since Rabari no longer remains the primary customer. Despite this, the products are still characterized by their classic motifs such as vakhiyo, chaumukh, satkani, hathi, dholki and many more, which are reminiscent of rural images created with the extra-weft method.
A blend of new and old, the modern-day Bhujodi consists of some wool from locally grown sheep. To meet the increasing demand, the Vankars also procure silk from Bangalore, acrylic from Ludhiana, wool from Badmere, and cotton from different places. They are now able to produce intricate and colourful designs as they use fine cotton.
For Injiri, It was difficult to find weavers and craftsmen who were ready to go the extra mile to work with design ideas on the loom. When Injiri visited the Bhujodi cluster in 2010 there was only production of saris, stoles, dupattas and shawls. It was the first time Injiri spoke of creating yardages with the weavers. The brand believed that handwoven fabric must be consumed for more contemporary usage in design such as home and fashion. There was an opportunity there to contribute to the world it felt closely associated with – the craft world. The brand commissioned a series of textiles from the weaver Shamji Bhai who was reluctant to produce yardages and it was a bit of a struggle to convince him. Shamji Bhai, who comes from a weaver’s family, always places traditions above everything else. His family has always been involved in weaving. From an early age, he had been learning weaving from his ancestors, who explained that though times may change and designs may change, tradition is important for a Vankar. The brand worked on various counts and various kinds of yarns. It experimented with the possibilities of the Bhujodi technique of weaving and came up with several kinds of fabrics. This was a starting point, and they never looked back. Having said that, it has been almost ten years and injiri has been weaving thousands of metres of yardages of several kinds every year with Shyamji’s family.
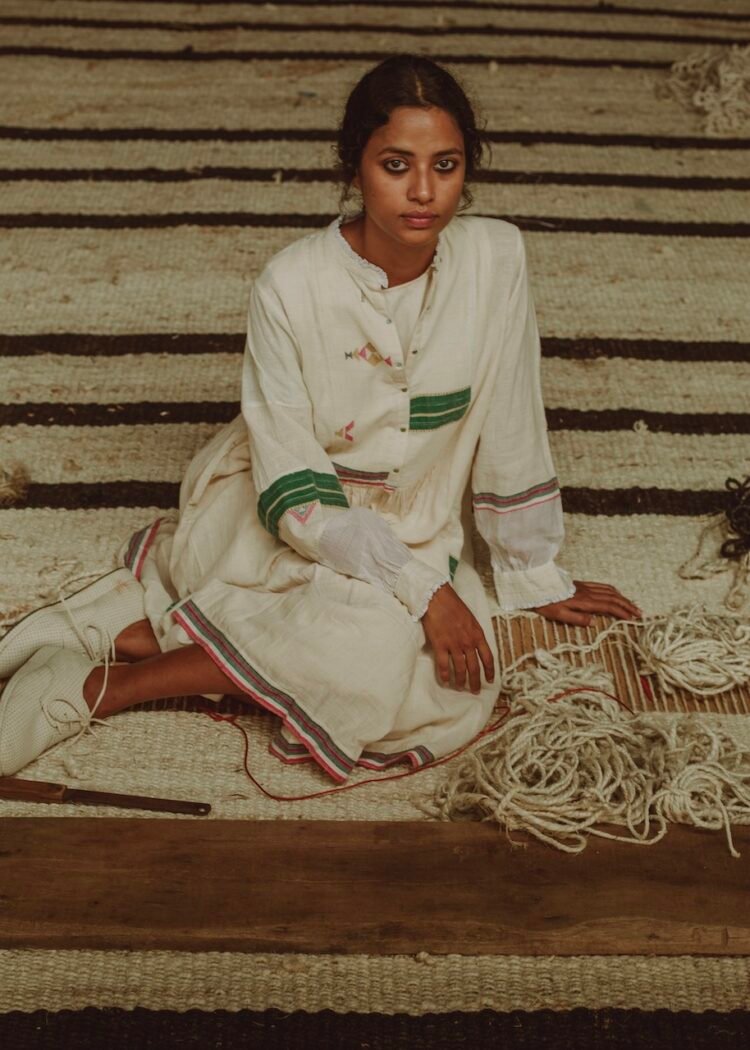